Le reazioni di Idrogenazione nell’Industria Chimica
L’idrogenazione è un processo fondamentale nella chimica organica industriale, con una vasta gamma di applicazioni e implicazioni. Volendo semplificare, potremmo definirlo come l’aggiunta di atomi di idrogeno ad una molecola organica al fine di convertire i legami insaturi, come i doppi e i tripli legami carbonio-carbonio, in legami singoli saturi.
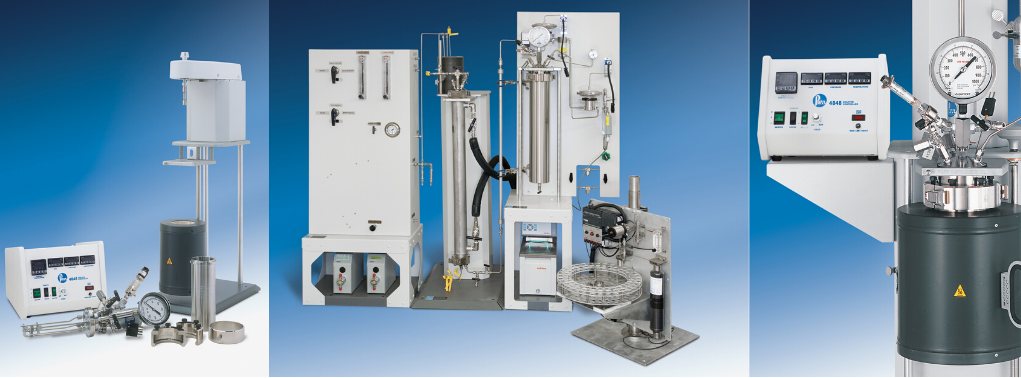
L’idrogenazione è sicuramente tra le reazioni più diffuse in moltissimi settori industriali, partendo proprio dalla chimica di base dove è fondamentale in alcuni processi produttivi come, ad esempio, la produzione di butano da oli o grassi vegetali o animali.
Questo tipo di reazione può essere eseguito in diverse condizioni chimico fisiche in virtù dell’obiettivo, dei reattivi in gioco e dai materiali coinvolti. Un classico esempio è l’idrogenazione catalitica che avviene ad una temperatura compresa tra 150 e 400°C (in base al substrato), ad una pressione tra i 150bar e 200bar e in presenza di un catalizzatore, solitamente un metallo nobile il platino, il rodio o il palladio.
Normalmente il metallo adsorbe sulla sua superficie sia l’idrogeno sia l’alchene. Questi si vengono così a trovare legati alla superficie del metallo e possono reagire in modo concertato. Il legame labile che l’alchene realizza inizialmente col metallo viene chiamato complesso π.
La reazione è una sin-addizione di idrogeno al doppio legame degli alcheni; infatti, i due atomi di H si legano sullo stesso lato del piano dell’alchene. Il meccanismo di reazione è radicalico.
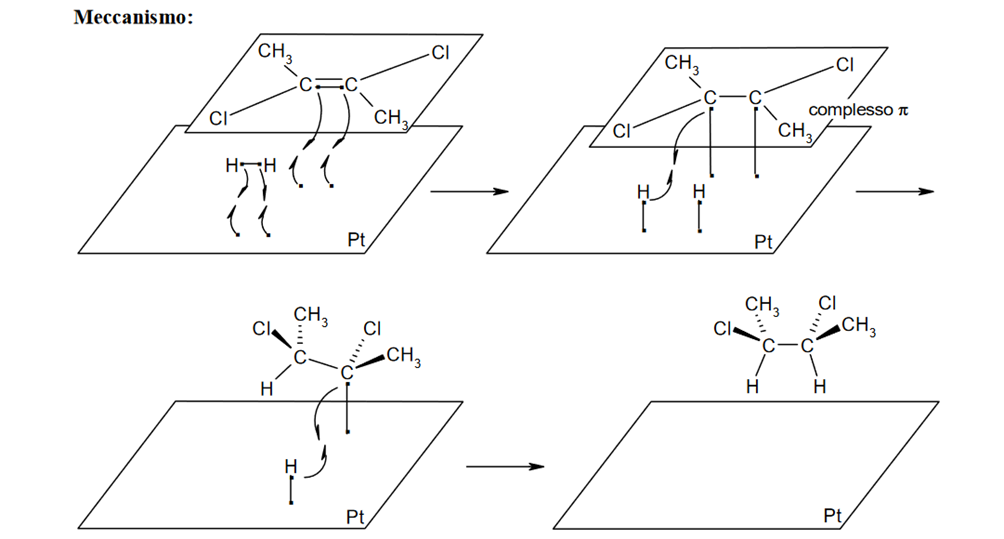
Nella produzione di oli lubrificanti l’idrogenazione gioca un ruolo fondamentale, perché permette di migliorare diverse caratteristiche chimico-fisiche: Per gli oli paraffinici, queste includono l’indice di viscosità, la resistenza all’ossidazione, la stabilità termica e la fluidità a bassa temperatura. Il prodotto che si ottiene dall’idrogenazione è più stabile termicamente e resistente all’ossidazione rispetto ad oli non lavorati.
Il processo permette di rimuovere composti aromatici e polari facendo reagire la materia con l’idrogeno in presenza di un catalizzatore a temperature e pressioni elevate.
L’idrogenazione catalitica permette di convertire gli idrocarburi aromatici in idrocarburi saturi e decomporre le lunghe catene di poliparaffine in idrocarburi saturi più leggeri.
La reazione avviene a temperature a 400°C e a pressioni di circa 200 bar e in presenza di un catalizzatore. I prodotti sono delle miscele di idrocarburi molto stabili che li rende ideali per gli oli utilizzati nella miscelazione dei lubrificanti.
Il processo di idrogenazione viene solitamente fatto in reattori in batch o in reattori tubolari continui.
I reattori tubolari continui più utilizzati nell’industria chimica sono definiti a letto fisso e consistono in reattore cilindrico montato verticalmente, che contiene un letto di catalizzatore sotto forma di particolato o compresse, supportati da una griglia nella parte inferiore del reattore. La fase liquida, introdotta nel reattore dalla testa, passa attraverso il catalizzatore dove va a contatto con l’idrogeno gassoso insufflato dal fondo. Questi reattori vengono utilizzati per massimizzare il volume di produzione rispetto ad un reattore in batch.
I reattori PARR possono rispondere in modo completo ed affidabile alla maggior parte delle richieste del mercato relative a reazioni di idrogenazione. Una delle caratteristiche che rendono PARR leader indiscusso nella costruzione di reattori è la possibilità di personalizzazione secondo le specifiche esigenze.
Ad esempio, è possibile insufflare l’idrogeno direttamente nel liquido tramite un tubo pescante, oppure attraverso un asta di agitazione opportunamente studiata per massimizzare il contatto gas-liquido. E’ anche possibile aggiungere dei catalizzatori in un cestello apposito, permettendo di massimizzare il contatto solido- liquido senza il rischio di perdere il catalizzatore. Questi sono solo alcuni esempi del grado di flessibilità costruttiva di questi sistemi.
Normalmente, il materiale standard per realizzare un reattore è l’Acciaio Inox T316 ma sono disponibili, su richiesta, leghe speciali quali Alloy 20, Alloy 400, Hastelloy C276, Nichel 200, Titanio grado 2, 3 e 4 e molte altre.
I reattori Parr sono disponibili in batch sia agitati che non agitati, con volumi compresi in un range da 25mL a 20L e anche tubolari continui, realizzati in varie lunghezze e diametri e progettati per lavorare alle condizioni operative per svolgere l’idrogenazione.
Monitoraggio di una reazione di Idrogenazione tramite NMR da Banco
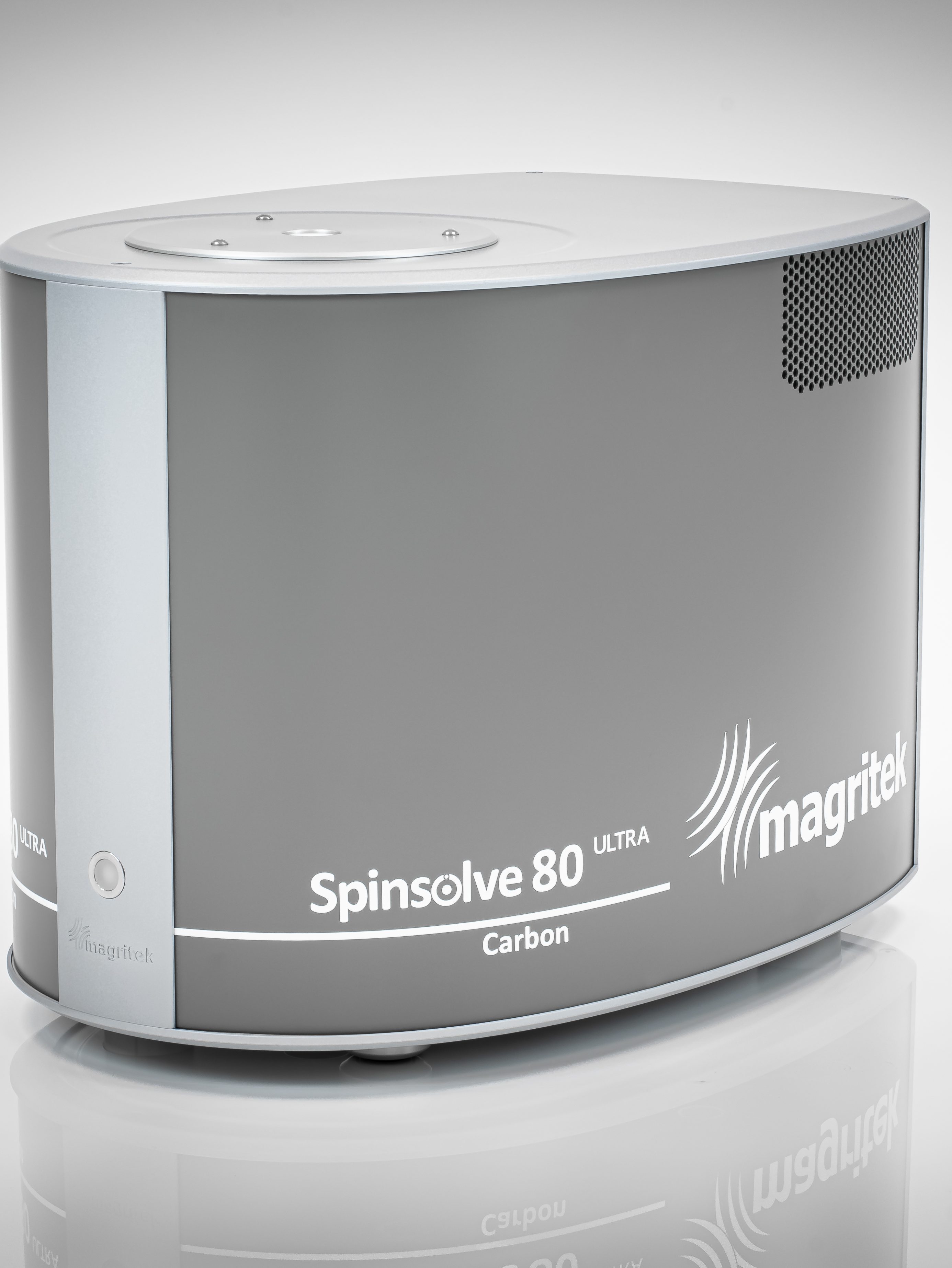
La sinergia tra i reattori a flusso continuo e la spettroscopia da banco di risonanza magnetica nucleare (NMR) ha attirato un’attenzione significativa negli ultimi anni grazie al suo impatto sulla sintesi e sull’analisi chimica. I reattori a flusso continuo offrono vantaggi distinti, tra cui un controllo preciso sui parametri di reazione, una maggiore sicurezza e una migliore efficienza della reazione. Al contrario, la spettroscopia NMR da banco fornisce informazioni quantitative e non distruttive sulla cinetica di reazione, sugli intermedi e sui prodotti finali. Questa integrazione consente il monitoraggio in tempo reale della conversione in funzione dei parametri del reattore, facilitando un’ottimizzazione della reazione rapida e persino automatizzata. I vantaggi di questo approccio ibrido sono evidenti nei processi accelerati di scoperta e ottimizzazione delle reazioni. I ricercatori possono utilizzare dati NMR in tempo reale per apportare modifiche immediate alle condizioni di reazione, con conseguente miglioramento delle rese e della selettività. Inoltre, l’analisi in linea riduce la necessità di laboriose preparazioni dei campioni e analisi offline, semplificando così i flussi di lavoro e riducendo al minimo gli sprechi.
La cinetica di reazione può essere monitorata continuamente utilizzando la spettroscopia 1H-NMR con soppressione del solvente utilizzando uno spettrometro NMR da banco Multi-X Spinsolve Ultra da 80 MHz dotato di un kit di monitoraggio della reazione 2 (RMK2). Questo kit include una cella di flusso in vetro che copre lo spettrometro dall’alto verso il basso consentendo il pompaggio continuo della miscela di reazione attraverso il volume sensibile di Spinsolve in modalità continua o a flusso interrotto.
Il modello Spinsolve ULTRA, da accoppiare al reattore, è uno spettrometro compatto che offre funzionalità ad alta risoluzione, fondamentali per acquisire spettri di prodotti disciolti in solventi protonati. I risultati dimostrano che integrando uno strumento analitico online rapido, come la spettroscopia NMR, è possibile esplorare a fondo l’intero spettro dei parametri in poche ore per ottimizzare la reazione.
Qualsiasi gas di idrogeno non reagito rimasto dopo il passaggio attraverso il reattore deve essere separato in modo efficiente all’uscita del reattore utilizzando per esempio un separatore di fase gassosa-liquida Zaiput “SEP-10”.
Per ottimizzare le condizioni di reazione, vari parametri (temperatura, pressione, quantità di idrogeno e portata del liquido) possono essere variati sistematicamente acquisendo continuamente gli spettri per identificare la combinazione ottimale di parametri.
Per quantificare le concentrazioni dei reagenti e dei prodotti, le regioni del segnale sono state integrate e può essere costruito contemporaneamente dal programma anche il profilo cinetico.