Reattori da laboratorio per processo petrolchimico
Simulare un impianto petrolchimico con l’utilizzo di reattori specifici è un’attività piuttosto complessa e che richiede una notevole esperienza. La configurazione di un reattore che risponda alle esigenze specifiche, in termini di condizioni chimico-fisiche e parametri da monitorare, è altrettanto complesso e delicato. Per ogni sito industriale, le esigenze sono spesso molto diverse e dipendono dal tipo di reazioni che vengono condotte. Tra quelle più utilizzate ci sono: reazioni di cracking, reforming, disbondig e reazioni di Fischer-Tropsch. Grazie alla grande esperienza PARR è possibile far fronte alla maggior parte delle esigenze andando a costruire il sistema più adatto in funzione della reazione da eseguire.
Cracking , reforming Termico e Catalitico e disbonding
Uno dei processi oggi più utilizzati per la raffinazione del petrolio è sicuramente il Cracking Catalitico a letto fluido (FCC) perché trasforma la frazione di gasolio pesante della distillazione primaria in prodotti finiti come Benzina e Gasolio.
Per migliorare la qualità della benzina e quindi aumentare il numero di ottano nel carburante si eseguono reazioni di reforming.
Altra reazione molto utilizzata è quella di disbondig effettuata per testare in atmosfera di Idrogeno materiali di origine metallica che lavorano in condizioni estreme. Anche per questa reazione vengono utilizzate condizioni di pressione e temperatura tali da controllare l’effettiva resistenza del materiale.
I reattori PARR possono rispondere in modo completo ed affidabile a tutte le esigenze che emergono in queste tipologie di reazioni. Tutti i parametri che abbiamo visto essere fondamentali per un corretto monitoraggio delle reazioni sono la base costruttiva su cui sviluppare e realizzare il prodotto adatto alle proprie esigenze. Una delle caratteristiche che rendono PARR leader indiscusso nella realizzazione di reattori è la possibilità di poter personalizzare ed ottimizzare i reattori secondo le specifiche esigenze. I vantaggi? Le dimensioni disponibili, i materiali costruttivi, la temperatura e la pressione di esercizio. PARR offre la possibilità di lavorare con reattori in batch sia agitati che non agitati dai 25ml fino ai 18.75 litri (i volumi si riferiscono all’effettivo spazio interno, ma per ragioni di sicurezza operativa, la massima quantità di liquido che può essere introdotta non dovrebbe mai superare i 2/3 del volume totale). I materiali di realizzazione di un sistema dipendono sostanzialmente dall’aggressività chimica delle sostanze in gioco. Normalmente il materiale di costruzione è Acciaio Inox 316 ma è possibile realizzare il reattore anche in leghe speciali quali: lega 20, lega 400, nichel 200, titanio 2&4 e molte altre anche realizzabili su richiesta. Normalmente la scelta della temperatura varia dai 350 °C con guarnizioni in PTFE ai 500 °C con guarnizioni in grafite. PARR inoltre offre un ulteriore sistema di chiusura del reattore dove è possibile utilizzare un O-Ring a chiusura rapida per usi generici fino ad una temperatura massima di 225 °C. Il riscaldamento del reattore può essere elettrico oppure a camicia utilizzando un sistema di termostatazione. Per quanto riguarda la pressione questa chiaramente è legata al volume del reattore. I reattori da 600 ml, ed inferiori, sono testati fino ai 3000 psi; mentre per i sistemi da 1 Litro a salire si dispone di una pressione massima di 1900 psi. Sono disponibili reattori per pressioni massime fino a 5000 psi per esigenze applicative più spinte. È comunque possibile personalizzare il reattore anche per pressioni più elevate.
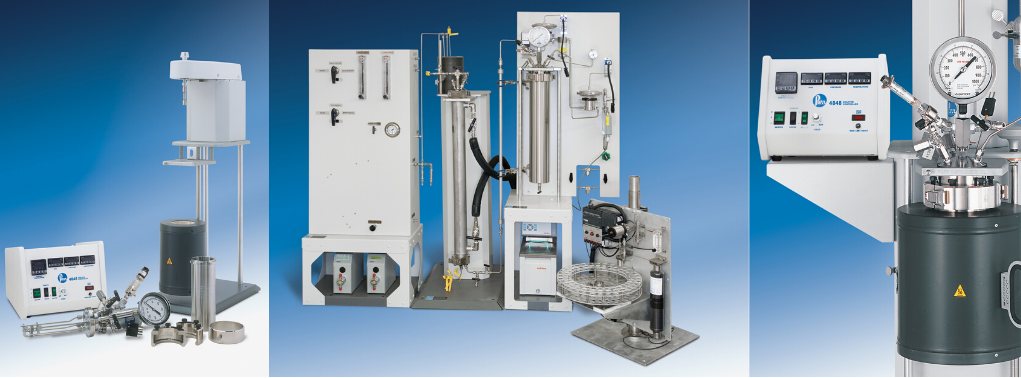
Reazioni di Fisher – Tropsch
Ultima reazione, ma non per importanza, è quella di Fischer-Tropsch che permette di convertire monossido di carbonio e idrogeno in idrocarburi di basso peso molecolare.
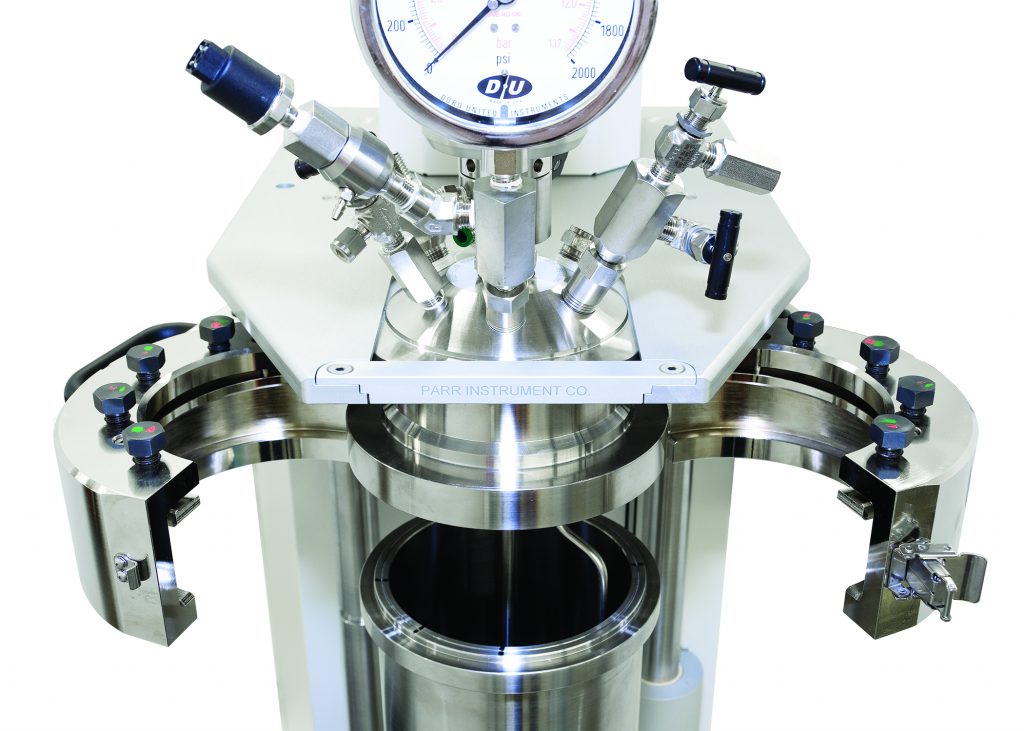
La reazione utilizza un catalizzatore a base di ossido di ferro o cobalto ed è innescata grazie ad una parziale ossidazione del carbone o del materiale legnoso. Il meccanismo è di tipo “a catena” e per ogni ciclo si ha un allungamento della catena alchilica fino al punto in cui avviene la reazione di rottura che porta alla formazione del carbonile originario, di acqua e dell’idrocarburo finale. Il sistema che permette di eseguire questa reazione è costituito da 3 reattori tubolari che possono essere configurati in parallelo, oppure in cascata in modo che il prodotto di un reattore finisca direttamente nel reattore successivo. Una delle caratteristiche uniche di questo sistema è la possibilità di miscelare fino a quattro composti gassosi in specifici sottosistemi controllati dai flussimetri dedicati. A valle di ogni reattore è inserito un sistema di scambio termico/condensatore, un separatore gas/liquido ed un regolatore di pressione completamente automatico.